Specialist Suggestions on What is Porosity in Welding and Just How to Address It
Specialist Suggestions on What is Porosity in Welding and Just How to Address It
Blog Article
Deciphering the Mystery of Porosity in Welding: Tips for Lessening Defects and Maximizing Quality
In the complex world of welding, porosity continues to be a relentless challenge that can substantially impact the quality and stability of bonded joints. As we delve into the depths of porosity in welding, uncovering the tricks to its avoidance and control will certainly be critical for specialists looking for to grasp the art of high-grade weldments.
Recognizing Porosity in Welding
Porosity in welding, an usual problem come across by welders, refers to the existence of gas pockets or spaces in the bonded material, which can endanger the honesty and quality of the weld. These gas pockets are usually caught throughout the welding procedure due to different elements such as incorrect protecting gas, infected base materials, or wrong welding criteria. The development of porosity can damage the weld, making it prone to cracking and corrosion, ultimately bring about structural failures.
By identifying the significance of preserving proper gas protecting, guaranteeing the tidiness of base materials, and enhancing welding settings, welders can substantially reduce the possibility of porosity formation. Overall, an extensive understanding of porosity in welding is necessary for welders to generate high-quality and resilient welds.
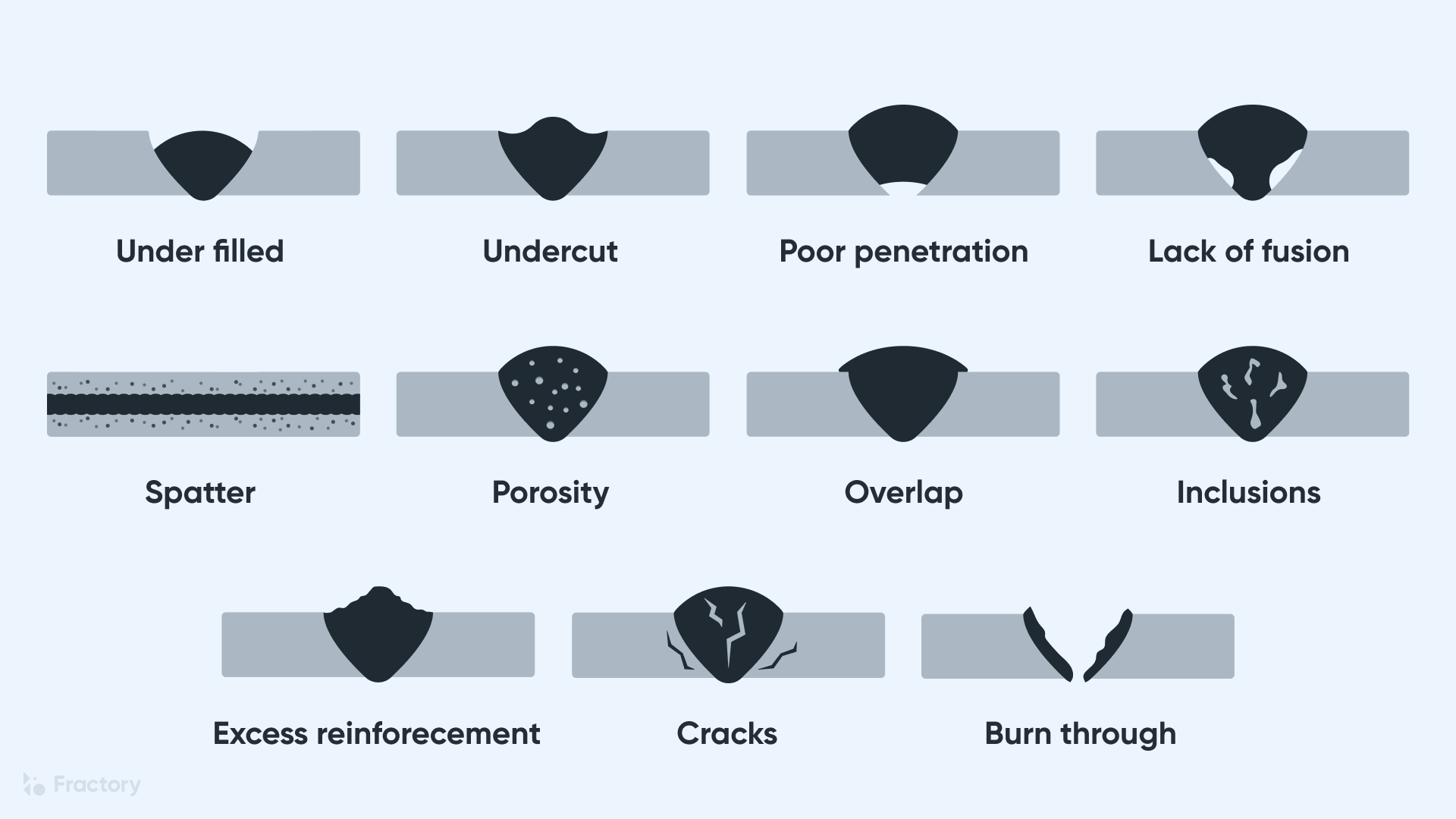
Typical Causes of Porosity
When inspecting welding processes for potential top quality problems, comprehending the typical reasons of porosity is crucial for keeping weld integrity and avoiding structural failings. Porosity, defined by the visibility of tooth cavities or spaces in the weld steel, can significantly jeopardize the mechanical residential properties of a bonded joint.
In addition, welding at improper parameters, such as exceedingly high traveling speeds or currents, can produce extreme disturbance in the weld swimming pool, capturing gases and creating porosity. By attending to these common causes through proper gas protecting, product preparation, and adherence to optimum welding parameters, welders can decrease porosity and boost the quality of their welds.
Techniques for Porosity Prevention
Executing reliable safety nets is crucial in lessening the occurrence of porosity in welding processes. One method for porosity prevention is guaranteeing correct cleansing of the base metal prior to welding. Impurities such as oil, grease, rust, and paint can bring about porosity, so complete cleaning using proper solvents or mechanical approaches is crucial.

An additional secret preventive measure is the selection of the ideal welding consumables. Making use of high-grade filler materials and securing gases that appropriate for the base steel and welding process can significantly reduce the danger of porosity. Furthermore, preserving appropriate welding specifications, such as voltage, existing, travel speed, and gas flow price, is essential for porosity avoidance. Differing the advised settings can result in incorrect gas protection and poor blend, resulting in porosity.
Moreover, using appropriate welding strategies, such as preserving a constant traveling speed, electrode angle, and arc length, can aid protect against porosity (What is Porosity). Ample training of welders to ensure they comply with finest practices and quality assurance procedures is also vital in reducing porosity issues in welding
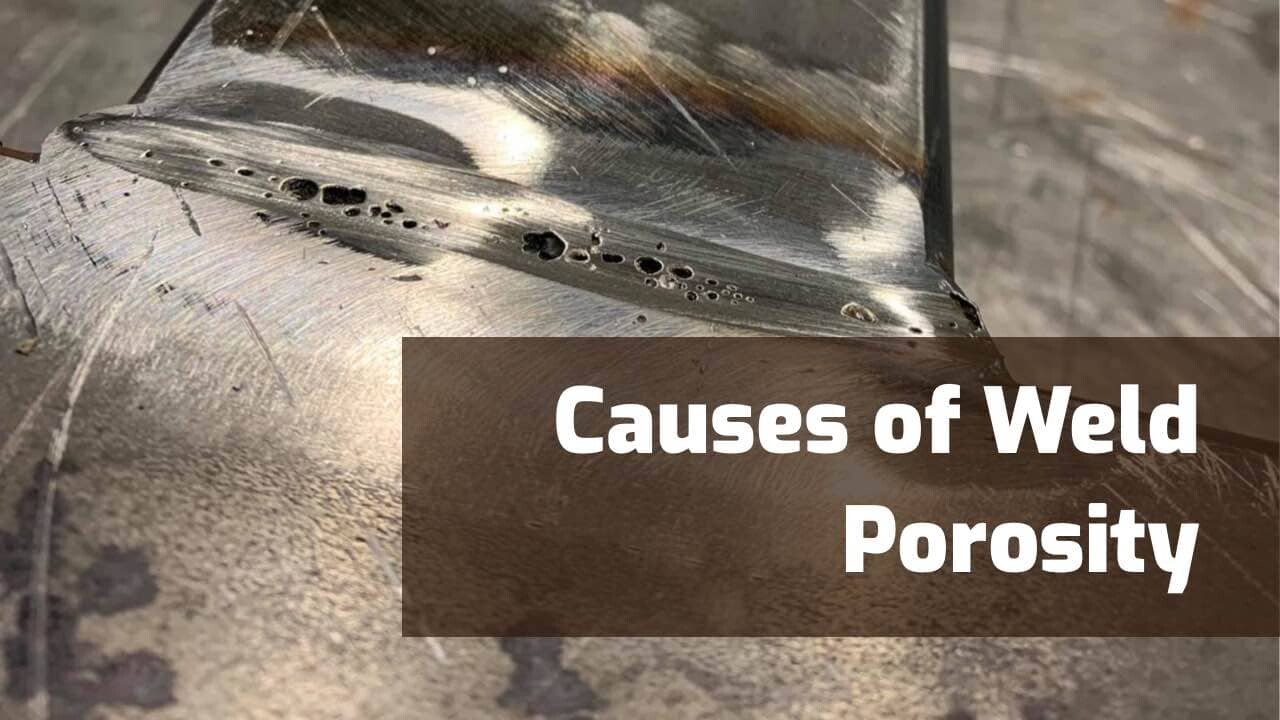
Finest Practices for High Quality Welds
Ensuring adherence to market criteria and correct weld joint preparation are essential aspects of achieving constantly high-quality welds. In enhancement to these foundational actions, there are numerous finest practices that welders can apply to additionally improve the quality of their welds. One trick practice is keeping proper tidiness in the welding location. Impurities such as oil, oil, rust, and paint can negatively affect the top quality of the weld, resulting in defects. Completely cleaning up the workpiece and bordering area prior to welding can assist reduce these problems.
An additional ideal technique is to meticulously select the appropriate welding parameters for the certain products being joined. Appropriate criterion selection ensures optimal weld infiltration, fusion, and total quality. Using high-grade welding consumables, such as electrodes and filler steels, can considerably impact the last weld top quality.
Importance of Porosity Control
Porosity control plays an essential function in ensuring the integrity and high quality of welding joints. Porosity, identified by the visibility of dental caries or gaps within the weld steel, can considerably compromise the mechanical residential or commercial properties and structural honesty of the weld. Extreme porosity deteriorates the weld, making it a lot more vulnerable to fracturing, deterioration, and general failure under functional lots.
Efficient porosity control is essential for keeping important link the wanted mechanical homes, such as toughness, ductility, and toughness, of the bonded joint. What is Porosity. By minimizing porosity, welders can enhance the general high quality and this link reliability of the weld, ensuring that it fulfills the efficiency demands of the designated application
Additionally, porosity control is essential for attaining the wanted aesthetic look of the weld. Too much porosity not just damages the weld but additionally diminishes its visual appeal, which can be critical in markets where looks are very important. Proper porosity control methods, such as utilizing the proper securing gas, controlling the welding criteria, and making sure correct tidiness of the base products, are crucial for producing premium welds with marginal defects.
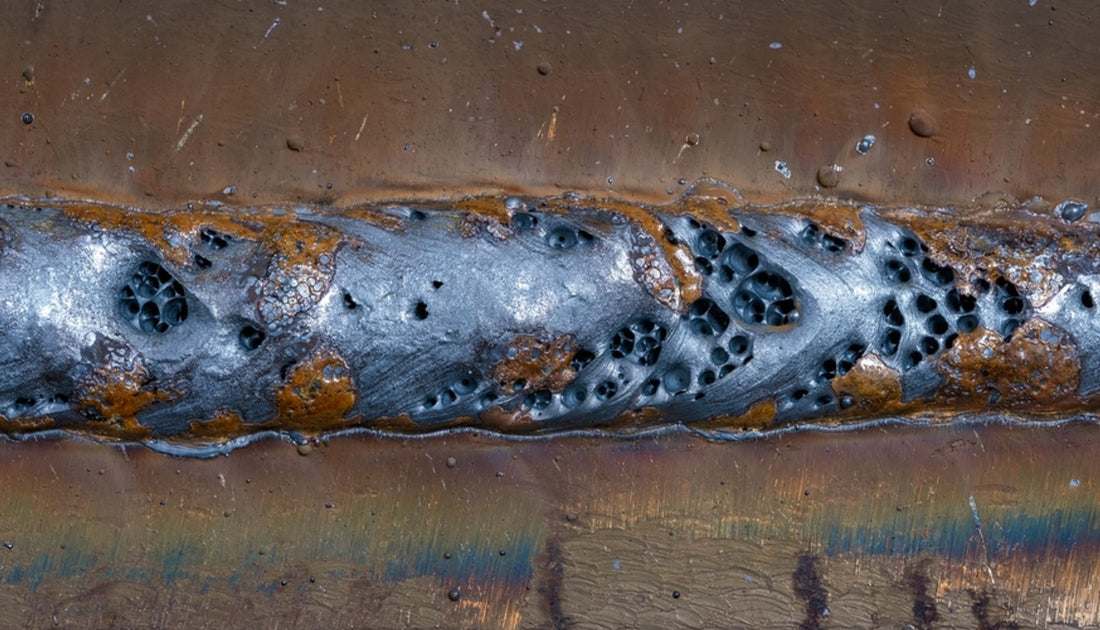
Conclusion
In verdict, porosity in welding is an usual defect see this page that can jeopardize the quality of the weld. It is crucial to manage porosity in welding to ensure the integrity and toughness of the last product.
Report this page